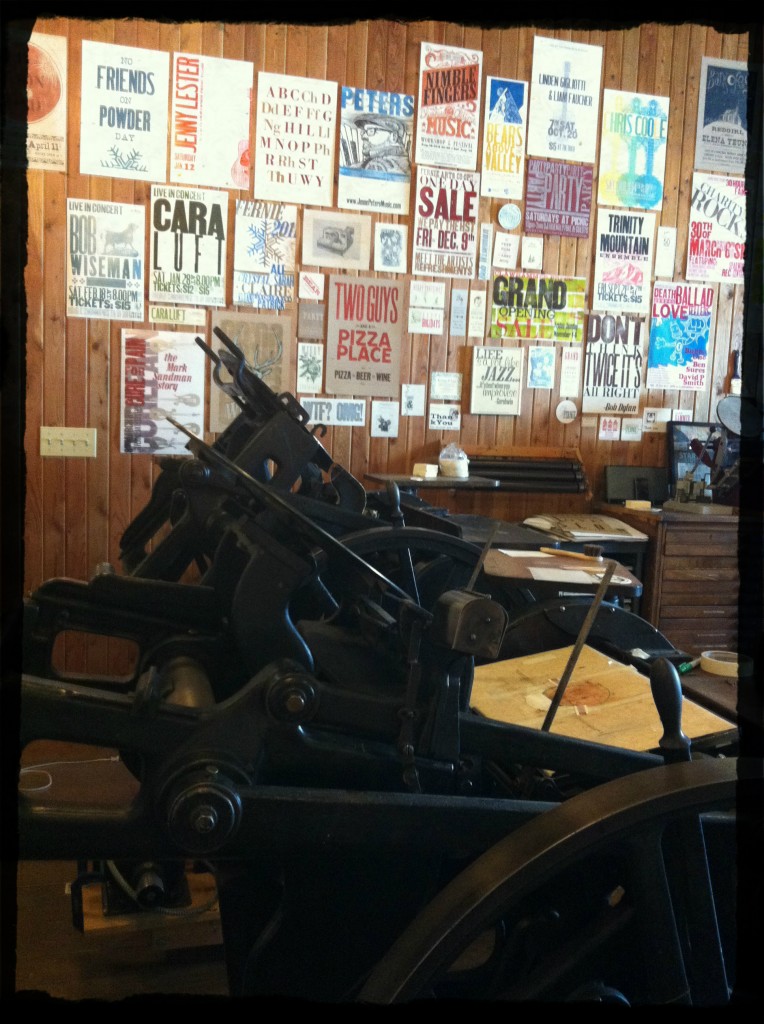
Allow me to introduce you to Clawhammer Letterpress. I went a travelling last week to Fernie, British Colombia, Canada. It was here that I met with Michael Hepher. He is the incredibly talented artist behind this letterpress shop.
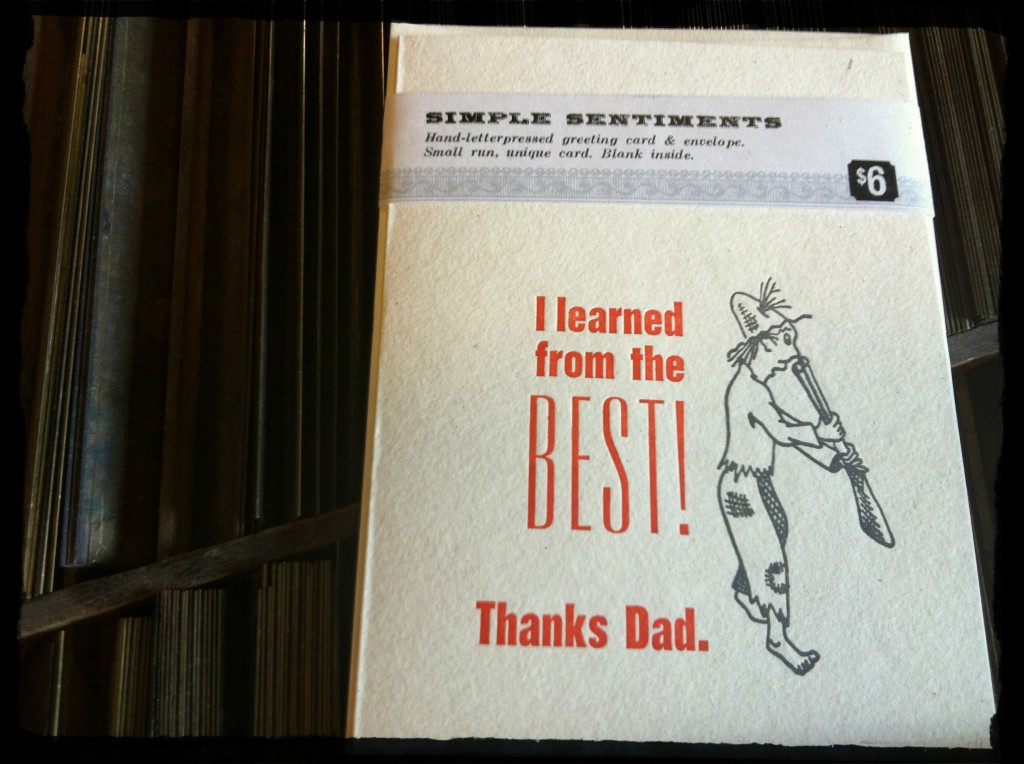
It will be just two years this August (2013) that Michael, once a graphic artist and blacksmith, opened up shop under the unusual name Clawhammer Letterpress. Unusual perhaps only to me, for if you are a musician, as Michael is (I told you he is crazy talented) you might know that the term claw hammer refers to a particular style of banjo playing. In this style the hand is in a claw like shape as it strikes the strings on the downward motion. There is a rich history between the hillbilly type of music that often features a banjo, the music as a means of communicating and the era of the letterpress.
Letterpress was the standard approach to printing since it’s invention by Johannes Gutenberg in the mid 15th century through to the 20th century. The letterpress technique creates the text by inking movable pieces of metal or wood, otherwise called “sorts”; each stamped with an individual letter or symbol (as in the drawer open below). The sorts are then pressed into the paper. It leaves a beautiful imprint, almost 3D in appearance and texture.
Each drawer is organized in the same way. A map if you like. All the letter “M’s” are always in the same spot and the little section that houses the letter “a’s” never moves. This is pretty key to be efficient at setting up your text as you need to grab the letters fast and be assured of grabbing the correct letter. As you can imagine some letters are used more often than others. So when the printer manually reaches for the “t’s” they would want to make sure there was enough “t’s” in that particular typeface to spell out the full document or text. If they ran out this could mean a major hiccup in completing the print job and would be very frustrating. This is where the common colloquialism “out of sorts” comes from!
In this photo, above, Michael is putting the individual sorts into a “composing stick.” The sorts, or letters, go in upside down so that when placed in the press the image on the paper will be legible.
The next step in the letterpress process is called “makeready” which involves inserting spacers in between your letters depending on where on the paper you want your text to appear. Then, once in a frame, pressure is applied to ensure the sorts don’t fall out when placed on the actual press.
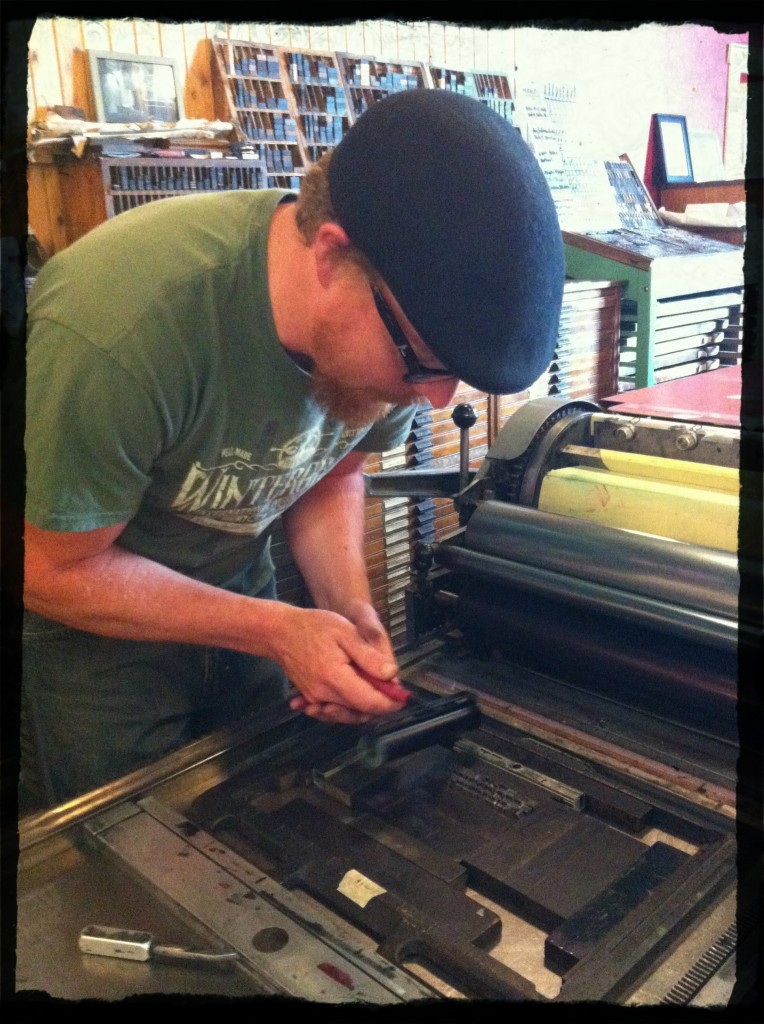
Just about ready to print! Here the ink is being applied before the paper will be rolled, or pressed, over the fonts. The finished piece is just beautiful! You can almost feel the texture and see how the pressed text sinks down into the paper. Lovely. Thank you Michael at Clawhammer Letterpress for sharing your knowledge, time and talent to show us a craft you so clearly love.
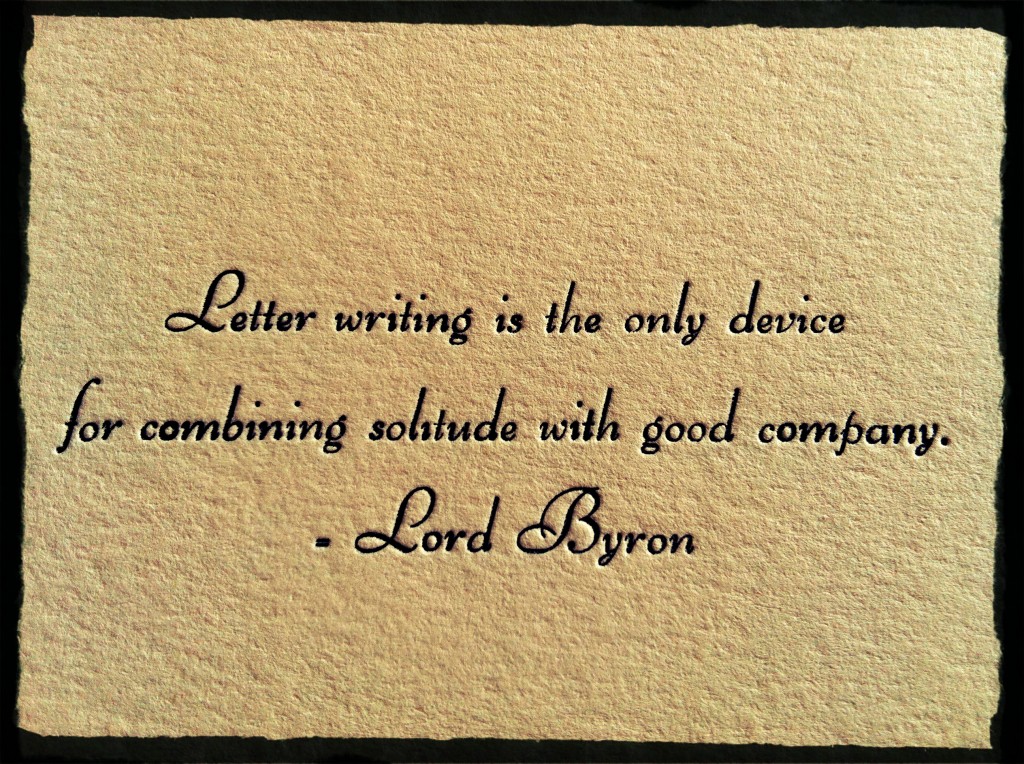
what a creative and interesting blog you have. loved reading your posts. Thanks for stopping by my blog the other day. so glad to find you
So happy you came over for a visit Jean and that you enjoyed what you found. Thanks for the encouraging words. I do hope you come back to visit often.
That is my Bro-in-law and Barb is NOT kidding when she says he is crazy talented (and patient!!)
Hello there Monika, quite the brother-in-law you got there! 🙂 I am also loving his CD- so is that your sister on lead vocals then? It was such a pleasure to visit Clawhammer Letterpress and you are right about the patient part (as I knew nothing about the art/process beforehand)! Hope you enjoy the blog. Thanks for stopping by.
My husband used to be in the printing business, so when I showed him these pictures, I got a whole lesson on this type of printing 🙂 – very interesting!
This is awesome Jeanette! I absolutely love the results of letterpress printing. So beautiful! Have a good weekend.